Cellulose is used in multiple applications and cellulose fibres in coatings of welding electrode is one of the oldest application for these types of additives. It improves the welding properties of the electrodes depending upon the type and structure of coating.
A cellulosic electrode covering consists of naturally occurring organic compounds, minerals and metallic oxides where a cellulose (wood pulp) is the primary constituent, normally 30-40% of coating. In their formation, the mixture of organic materials and metal oxides are bonded on the core wire with the help of binders. These coatings on melting, gives sound weld protection along with the formation of slag. Besides some limitation on their usage, there are some factors that make them exceptional in intricate applications.
Following types of coating is used during production of welding electrodes
- A = acid coating
- B = basic coating
- R(B) = rutile with basic elements
- C = cellulose
- R(C) = rutile cellulose
- RR(C)= rutile cellulose, thick coating
- R = rutile coating
- RA = rutile-acid coating
- RR = rutile, thick coating
- RR = rutile basic, thick coating
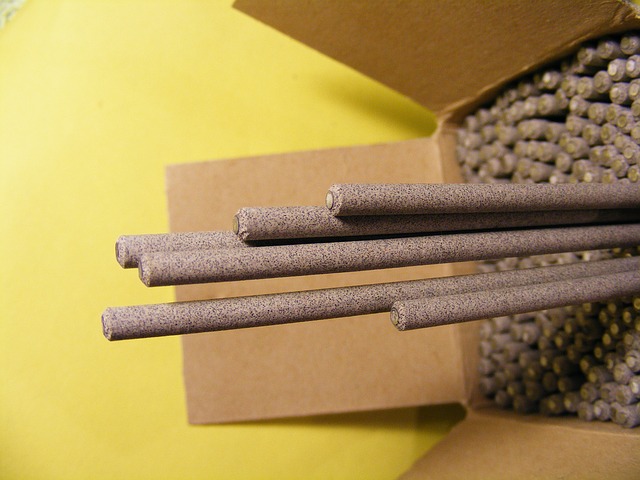
The stability of the arc, the material transfer during welding as well as slag and weld pool viscosity changes, depending on the composition and thickness of the coating used during production.
During welding, cellulose gets burned and form carbon dioxide, as inert gasses and protect the weld from oxidation. Cellulosic coatings as others types of coating used, produce less slag (burns completely) and hence are suitable for all welding positions. Cellulose electrodes are used for vertical-down welding, and especially for circumferential welds on pipelines. Cellulose ensures that a significant amount of material is molten during welding and a high penetration is achieved.
Mixed cellulose electrodes, these electrode types positively affect the melting properties and material transfer.
ADVANTAGES
- Sound Gas Shielding
- Arc Characteristics
- Electrode Polarity
- Best for root pass
UNIQUE FEATURES of Weldcel
- High Arc Voltage
- Ease of removing slag
- Welding in Vertical down Position
- Formation of Hydrogen
STANDARDS | SPECIFICATIONS |
Description | White or Granular, White or almost White Powder |
Alpha Cellulose % by mass | NLT 80 |
Degree of Polymerization | 200 – 700 |
Moisture Content % by mass | NMT 7.0 |
Ash % by mass (on dry basis) | NMT 5.0 |
pH | 6.0 to 8.0 |
Bulk density, g/cc | 0.10 – 0.50* |
In-house Specifications* | |
Particle Size % | |
Passing 100 Mesh | NLT 70* |
Storage Conditions: Store Protected from Light and Moisture.
Re-evaluation Date: Four (4) years from date of manufacture, if storage conditions stated above are observed.
* Can be tailored to complement desired performance.
When using our products, please note that the processing conditions and declaration options depend on the specific composition and positioning of the end product and must, in particular cases, also be assessed in due consideration of product and country-specific regulations.
Available Packaging Type
Type | Size |
HDPE Bags | 25 Kg |
HDPE Bags | 20 Kg |
Paper Bags | 25 Kg |
Paper Bags | 20 Kg |
FIBC | 300 Kg |
*Our standard packaging is in 25 kg Bags. We can also customize packaging as per customers request at additional cost.
Container | Palletized | Non-Palletized |
---|---|---|
20 Ft. (Approx Wt.) | 10,000 Kg | 12,000 Kg |
40 Ft. (Approx Wt.) | 20,000 Kg | 24,000 Kg |